2-D + 3-D = 5-Axis Waterjet Cutting
The cutting technology is a gateway to new fabricating opportunities
5-Axis Waterjet Cutting is not something you see in every fabricating operation. But for some applications where tube or precise edge cutting might be required, it makes total sense.
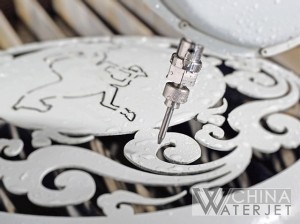
Figure 1: One of the things for which articulated cutting heads can be used is to compensate for the natural taper that occurs with a waterjet stream.
While five-axis operations such as bevel cutting and other weld prep operations have been possible on abrasive waterjet machines for some time, the capability to process 3-D parts such as tubes and pipes on the same waterjet is relatively new. This is opening up new possibilities for metal fabricators.
Shops that once focused primarily on flat 2-D work now have the opportunity to take on 3-D work with one five-axis abrasive waterjet machine. And those shops specializing in tube and pipe fabrication can now process their 3-D cylindrical parts on the same type of machine. Additionally, that same five-axis abrasivejet machine allows fabricators to process flat 2-D parts, such as gussets and supports, that may have been previously farmed out to other shops.
Because abrasive waterjet machines cut practically any material, fabricating shops with five-axis machine capability can broaden their markets in terms of the materials they are able to process. Shops can waterjet-cut glass and help customers avoid the headaches associated with machining these types of brittle materials. The waterjet, without the use of abrasive, can be used to cut rubber gaskets and forms much more quickly and cleanly than conventional cutting equipment. The waterjet, using low-pressure piercing, also can cut stone for architectural or decorative purposes.
In some instances, shops can easily and cost-effectively upgrade their existing bridge-type 2-D abrasive waterjet machines by adding software, articulating heads, and rotary units to obtain full 3-D cutting capabilities.
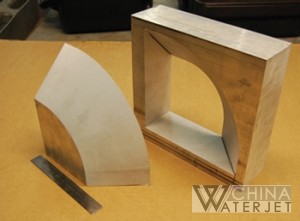
Figure 2: Most of the time bevel cuts are for weld prep. However, when a very deep bevel is needed for a large part, a five-axis abrasive waterjet can handle that job as well.
Exploring the Articulating Head
Articulating heads (see Figure 1) are the key to five-axis waterjet cutting. In addition to a machine’s X, Y, and Z axes, articulating heads provide two tilt angles—one perpendicular to the X axis and the other perpendicular to the Y axis.
Some articulating cutting heads were initially developed for making beveled (see Figure 2) and angled cuts. With the advancements in machine control software, articulating heads now can perform taper compensation to further improve cutting accuracy.
Some articulating heads work within the safety limitations of abrasive waterjet cutting (see Within the Limitations of Safety sidebar). While there are five axes of motion, the range of the two tilt axes is controlled to a specific limited distance so that the abrasive waterjet stream is always shooting in a generally downward direction toward the machine’s water tank.
Cylinder Cutting on the Waterjet
Currently the most common use of 2-D machines with added articulating cutting heads is for bevels associated with weld prep and miter cuts for parts that intersect at an angle. They also are used to cut countersinks on large holes.
When a bolt-on rotary axis unit is paired with an articulating head (see Figure 3), the combination gives fabricating shops the ability to perform five-axis operations on tubes, pipes, and other cylindrical parts. Such operations include cutting fish-mouth shapes and other end shapes necessary to join tubes or pipes to one another (see Figure 4).
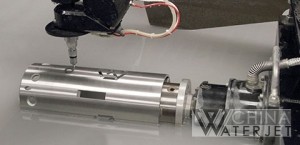
Figure 3: The combination of an articulated cutting head and a rotary chuck allows fabricators to use a waterjet for intricate tube cutting.
Software Makes 5-Axis Waterjet Cutting Work
Articulating heads and rotary units provided the machine motion needed for five-axis waterjet cutting, but improvements in machine programming really advanced the cutting capability (see Figure 5). Early on parts could be programmed manually, but the task was very involved and extremely time-consuming. Today, however, developers have created software specifically to support multiple-axis, coordinated machine motion and 3-D part processing. With this software, shops can quickly and easily program and cut 3-D patterns for several applications, from the peripheries of tubes and pipes, to fitting operations, to prep cuts and bevels.
To make these waterjet cutting machines even more user-friendly, advanced control software has a multitude of tube- and pipe-cut subroutines embedded in the machine control. How easy is it to use? If an operator wants to program the machine to cut a cylinder, he calls up the control’s subprogram screen. The operator then enters the two diameters of the cylinders being joined, as well as the desired angle of intersection. From there the software automatically performs all the necessary calculations.
Leading programming software for these types of five-axis machines often can link to other common CAD/CAM systems. This allows shops to program machines in software packages that they are already comfortable with and using. The CAD files are then transferred to the machine control software and directions are produced for proper machine movement.
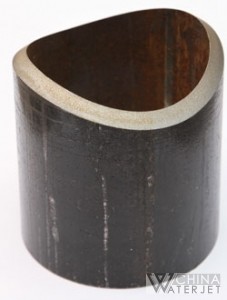
Figure 4: The cut may not look exotic, but the ability of a five-axis abrasive waterjet to deliver precise end cuts on a tube or pipe is very important in some industries where first-time fit-up could be the difference between a profitable and unprofitable job.
What Parts Make the Most Sense?
While technology advancements have simplified five-axis cutting, certain factors must be considered before moving a part over to the abrasive waterjet table.
Workpiece shapes, for example, can limit the use of five-axis cutting. Shops must be cognizant of exactly where an abrasive waterjet stream will be pointing, especially when cutting angled features such as countersinks on holes. If the angle of the countersink is too small or the corresponding hole diameter is not big enough, the waterjet will cut into the opposite side wall of the hole. Visualize countersinking a 0.5-in.-diameter hole in a 3-in.-thick part as compared with countersinking a 3-in.-diameter hole in a 0.5-in.-thick part.
Most fabricating shops work with part material thicknesses of 2 in. or less. In most instances, five-axis waterjet cutting is used to create bevels and angles that are 0.25 in., 0.375 in., or 0.5 in. wide. Making such cuts on an abrasive waterjet eliminates having to generate them in secondary operations using other pieces of equipment.
As far as tube and pipe cutting is concerned, the main restriction to five-axis abrasive waterjet cutting is inside diameter (ID) size. The smaller the ID of a tube or pipe, the greater the risk is of the abrasive waterjet stream cutting into an opposite part side wall while processing an end or side. To prevent such an occurrence, pieces of ceramic can be inserted into the tube or pipe that deflect the waterjet stream and prevent it from cutting the opposite part surface. The use of a deflector applies only if the part ID is big enough. A 0.062-in. part ID, for instance, would not provide enough room for a deflector.
Today fabricating shops typically consider five-axis abrasive waterjet cutting for processing mostly short lengths of tubes and pipes with diameters of 1.5 in. and larger. The bulk of these types of parts are used for interconnecting spaceframe structures.
However, introductions of larger abrasive waterjet table sizes are enabling shops to process longer tubes and pipes. Because minimal force/torque is involved in the rotation of parts, the fabricator really only has to be concerned with providing a steady rest for supporting the long part.
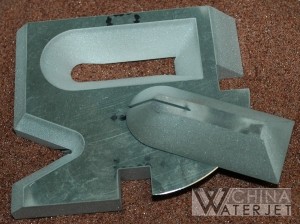
Figure 5: Several years ago, programming a waterjet to cut a complex part with multiple sharp angles and bevels could have taken a long time. Today advanced machine control software makes the job easier by simply taking the CAD file and creating the cutting path in seconds.
Fabricating for the Future
As more fabricating shops adopt five-axis abrasive waterjet cutting in an attempt to diversify their businesses, many industry experts foresee the technology being used to cut new kinds of materials—not just metals. Such a capability will prove extremely beneficial as more component designs incorporate less metal and more composite-type materials.
As manufacturing materials and part designs continue to change, fabricators must consider which technologies will increase their manufacturing versatility. Fabricating shops wanting to remain relevant in the next 20 years will be those that continue to adapt the latest technologies, such as five-axis abrasive waterjet machines.
Figure 3: The combination of an articulated cutting head and a rotary chuck allows fabricators to use a waterjet for intricate tube cutting.
Within the Limitations of Safety
A true five-axis machining system is one that moves and cuts in any direction. But in the case of abrasive waterjet cutting, doing so raises an important safety issue.
Abrasive waterjet streams pack a lot of power, even after cutting through a part surface or periphery. So where the stream is pointed and where it goes next must be carefully considered. Plain waterjet streams break down quickly in the air, but the abrasives in an abrasive waterjet stream do not dissolve and will continue moving at a high rate of speed. This fact is why abrasive waterjet machine OEMs are required to work within safety limitations and restrict the movement of articulating heads for five-axis machining.
While true 5-axis waterjet cutting systems have been around for some time, they have been housed in special containment rooms or enclosures lined with either concrete or steel to prevent the abrasive waterjet from wearing out the walls. Within these systems, a stand-alone robot hanging from the ceiling points the abrasive waterjet in any desired direction. Because of safety concerns, machinists are not able to be in the contained area while the system runs.
As opposed to a dangerous, true five-axis abrasive waterjet, modern articulating head movement is limited to any angle within specific safety parameters. These machines still provide five-axis movement, but the abrasive waterjet stream cannot be programmed to move into a position other than generally downward toward the machine’s water tank.